The calcium silicate board equipment includes a series of calcium silicate board production lines. What equipment does the calcium silicate board production line need? The calcium silicate board production line is configured differently according to the processing technology and annual output. Flowing method calcium silicate board production line equipment: pulp processing system, pulp section, plate stacking and demoulding section, pressure steam curing section, edge grinding and chamfering sanding section.
There are mainly the following methods for the production of calcium silicate board:
1. Flow slurry method: The principle is that the slurry is spread on the blanket and dewatered and laminated; the equipment requirements are simple and the output is low.
2. Copying method: The principle comes from the rotary screen papermaking process; the equipment requirements are high and the output is high.
3. Extrusion molding method: semi-wet production is adopted, and pressure extrusion is used to form the required shape; this method is rarely used in China.
The above three methods are mainly copy method and flow method. For details, you can consult Fang Ruizheng and technicians according to the raw materials and output of calcium silicate board produced. We will design suitable production lines and equipment for you free of charge. Configuration.
How much is the calcium silicate board production line? About 2.7 million yuan-12 million yuan, this calcium silicate board production line equipment quotation is for reference only, please contact Fang Ruizheng and sales staff for details, we will provide you with new product prices and design a reasonable production line and equipment configuration for you.
How much power does the calcium silicate board equipment require? 600 kilowatts. General users need to match a voltage transformer of more than 500 kilowatts.
How much space is needed to start a calcium silicate board production plant? To use Fang Ruizheng and calcium silicate board production equipment requires about 5,000 square meters, 70-80 meters long, 8-10 meters wide, and 8 meters high. For details, please contact Fang Ruizheng and technicians. We will design suitable silicic acid for you. Calcium board production line and equipment placement.
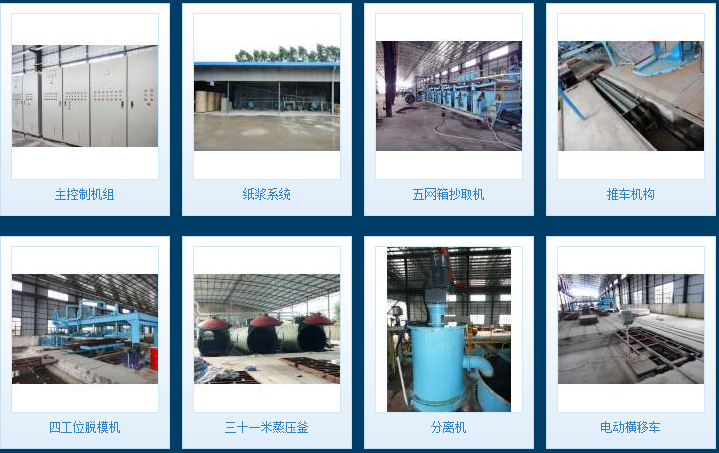
The production process of calcium silicate board flow slurry method:
1. Raw material preparation
The preparation of raw materials includes the wet grinding and pulping of quartz sand, the crushing and digestion of quicklime, and the grinding and beating of wood fibers.
2. Pulping process
The wood fiber pulp that has been diluted and pulverized to meet the beating degree is pumped into a counter-current mixer, and metered slaked lime, cement, quartz powder, etc. are sequentially added, and the counter-current mixer is fully mixed to make a certain concentration of slurry and pumped to the storage The slurry tank is reserved, and then it is homogenized by a single-disc refiner, stirred in a pre-mixed tank, and fed into the slurry plate making machine with a certain concentration and flow rate to enter the plate making operation.
3. Flow slurry board
The slurry that flows out evenly from the headbox is filtered and dehydrated on the running industrial blanket to form a thin layer and wound on the forming cylinder. When the thickness of the slab is reached after multiple layers of winding, the control system is designed according to the slab. The size is automatically cut off the slab. The plate making machine uses a forming cylinder with a diameter of 1600mm, and the slab is cut and trimmed horizontally to form two standard plates. The standard slabs are stacked with a stacker, and the stacking adopts a stacking method of one steel mold and one plate.
4. Plate compaction
The formed slab is pressurized by a 7000t press for 30 minutes, and the slab is dehydrated and compacted under a high pressure of 23.5MPa to improve the strength and density of the plate.
5. Pre-cultivation and demoulding
The wet slab is pre-cured in the pre-curing kiln, and demoulded after the slab gains a certain strength. The pre-cultivation temperature is 50~70℃, and the pre-cultivation time is 4~5h.
6. Autoclaved curing
After the slab is demolded, it is sent to the autoclave for autoclave curing for 24h, the vapor pressure is 1.2MPa, and the temperature is 190℃. During the steam curing process, the silicon dioxide, calcium hydroxide and water in the slab react chemically to form tobmullite crystals and xonotlite. The quality of the hydration reaction directly affects the strength, expansion ratio and moisture resistance of the calcium silicate board.
7. Drying, sanding, edging
The steam-cured slab is dried on the comb dryer in the tunnel kiln, so that the moisture content of the slab reaches the acceptance standard of not more than 10%. The slab can be delivered after sanding, edging and quality inspection.
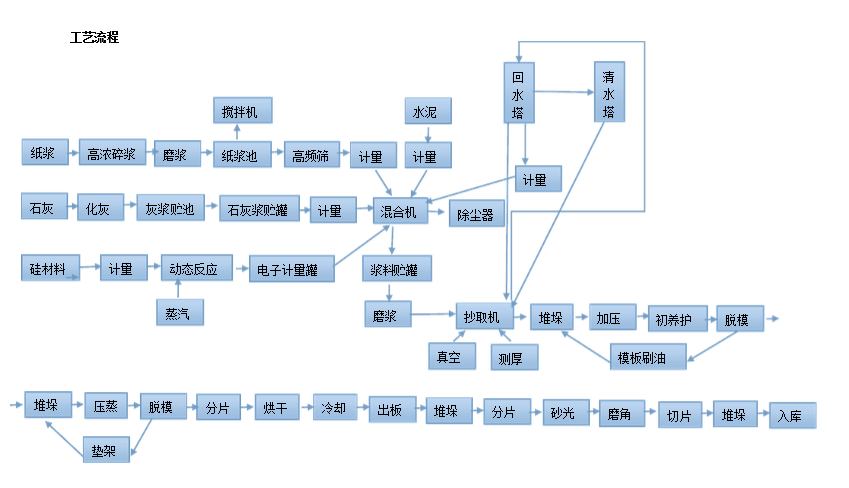
Advantages of calcium silicate board processed by calcium silicate board production line:
1. Fireproof, waterproof, moisture-proof, sound insulation, heat insulation, corrosion resistance, high strength
2. Anti-vibration, anti-collision, anti-ultraviolet, anti-weathering, anti-static
3. Easy to clean, durable in use and long life
4. Safe, green, environmentally friendly, economical, and easy to construct
5. Deep processing can be carried out on the base board, with strong customization.
The main raw materials for the production of calcium silicate board are: siliceous materials can be quartz sand, diatomaceous earth, fly ash, sand dust, china clay, etc., calcium materials can be quicklime powder, lime paste, slaked lime powder, calcium carbide mud, etc., and reinforcing materials can be used Wood paper fiber, wollastonite, glass fiber, mica powder, cellulose, organic synthetic fiber and asbestos fiber.
Raw materials and formula for making calcium silicate board:
1. Lime powder 10% + cement 50% + quartz powder 10% + wood pulp fiber 15% + wollastonite 5%
2. Silicon powder + calcium powder + natural log pulp fiber
The scope and main purpose of calcium silicate board:
Commercial buildings: commercial buildings, entertainment venues, shopping malls, hotels
Industrial buildings: factories, warehouses
Residential building: new type of residence, decoration and refurbishment
Public places: hospitals, theaters, stations
High-rise buildings: Forced to fire, corresponding to fire extinguishers and sprinkler systems.
Calcium silicate board is mainly used for industrial panels such as walls, suspended ceilings, floors, furniture, road sound insulation, sound-absorbing barriers, ship compartments and air ducts, and sound-absorbing walls, sound-absorbing ceilings, pouring walls, and composite wall panels. Panels and other fields.